We have reached a key moment in the energy transition. Regulators, system operators, standardization bodies, and research institutions have reached consensus that a decarbonized system will necessarily consist of inverter-based resources (IBRs) and that an inverter-based system needs grid-forming (GFM ) technology to be stable. In line with this understanding, there has been significant development in GFM controls, such as the demonstration of increased control stability in severely weak grid conditions and fast inertia control to stabilize frequency.
Challenges Along the Path
These represent advantages that could be designed into our system; however, we currently lack a clear definition of the characteristics and translation of the value created for both grid operators and equipment owners. Fundamental questions remain open, such as, how can grid companies and regulators set reasonable requirements for GFM equipment without manufacturers first knowing what design characteristics and performance metrics are needed to solve grid needs? Furthermore, how will manufacturers be incentivized to develop GFM equipment while still proving its viability, and how will renewable generation developers be incentivized to install potentially more expensive equipment without market mechanisms that compensate for the added value? An approach to answering these parallel—yet interdependent—questions may lie in a recently established initiative: the Global Power System Transformation Consortium’s (GPST) GFM Technology Council, where OEMs, grid companies, and equipment owners collaborate to define system needs, demonstrate equipment performance characteristics via pilots, and work with system operators and regulators to balance requirements and incentives (e.g., services markets) to deploy needed characteristics.
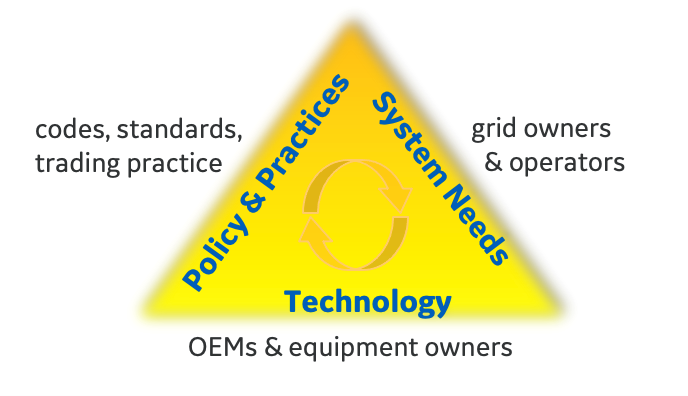
Source: GE
Regulatory challenges to GFM equipment development and adoption are rooted in questions around whether GFM capability should be required for some or all resources, and if so, who bears the cost of the development and capability? Regulators typically favor technology-agnostic requirements to avoid picking winners and losers, but this is very difficult to do in this case because IBR characteristics are different than synchronous technologies. Regulators need guidance from OEMs to account for possible, reasonable, and cost-efficient design to avoid gold-plating but support future proofing. Regulators also need guidance from grid operators to identify future scenarios and risks that need to be resolved. And lastly, regulators need input from equipment owners to equitably account for return on investment.
Evolution of Requirements
Growing awareness of the need for GFM solutions is sparking a burst of standards and code development activity. The UK was the first region acting on this need with the approval of GC0137 , which provided a specification for the provisioning of GFM capability. Others are following suit, and many other groups have started activities to define or standardize GFM controls. But without a push for these efforts to be coordinated, there is a real risk that equipment manufacturers will not be able to keep up with so many activities. Uncoordinated codes and standards development could lead to multiple outcomes that are impossible for one technology to satisfy. In the spirit of the GPST Technology Council, a more efficient approach would be to join forces and coordinate development efforts to identify solutions that are more aligned and practical to meet around the world.
Making It Real
Testing and demonstration also pose new challenges for GFM equipment developers, especially due to the need to assess large signal performance, such as dealing with grid faults. Typically, testing done during any equipment design phase starts in the lab utilizing grid simulation software with a focus on the individual piece of equipment. However, this is not sufficient to demonstrate the full potential of GFM functionality/behavior needed during highly stressful grid conditions and during faults when many IBRs need to work successfully together in an area to support stable recovery. A more practical approach for equipment developers to speed up development and deployment would be to build confidence with system operators to (1) allow renewable plants to participate in system service markets, and (2) increase comfort level more quickly with new IBR-related technologies, like GFM, and allow these technologies to be deployed on their systems with simpler grid interconnection processes.
While it has become generally accepted that GFM solutions will create value across the transforming power system, these value metrics will be highly varied. One source of variation comes from the fact that different systems have different risks and priorities that drive value for different capabilities of GFM solutions. For example, some high-penetration grids like in Texas and Australia need to have stable controls to avoid interactions and recover from faults in severely weak grids with high impedance networks and low short circuit ratios. Other systems, such as in Ireland, are more in need of frequency support and inertia as a priority. Great Britain offers a third example where inertia, dynamic voltage support, and supply of short circuit infeed to strengthen the grid is needed.
Not all IBRs are created equal in their capability to provide GFM or their costs to deploy services to resolve these various needs. This leads to the second source of variation of value metrics—the resource type that hosts the GFM solution. Battery storage and solar, in some ways, have fewer constraints than other IBRs since there is less potential for stress on equipment. However, storage alone is not a generation resource and lives by a separate set of economics. GFM wind generation has the additional challenge of managing drivetrain mechanical stress that may require additional hardware. GFM flexible AC transmission systems (FACTS) (including STATCOMs) are being specified in Europe, and voltage source converter (VSC)-type HVDC technology is largely considered GFM, with GFM requirements still being crafted. Until now, most of the research and literature relative to GFM controls has been around algorithms that control the grid interfacing of the converter, for the most part ignoring what is behind the DC link and any related potential constraints.
Roadmap for Success
Given the broad range of regulation, requirements, system design, testing, demonstration, and value that represent the GFM scene today, it will be crucial for the industry to rally around a clear taxonomy to simplify the landscape to make it clear that not all GFM is the same and not all IBR equipment can be treated equally to supply all services.
A simple taxonomy that we are using within GE separates GFM into two levels. The first level or “grid forming base” refers to the implementation of GFM algorithms on the converter—allowing it to operate as a voltage source and strengthen the grid. The second level, referred to as “grid forming plus,” relates to the technology powering the converter, for example, using energy storage to enable a higher level of GFM contribution, resulting in higher system performance.

Source: GE
Successfully deploying GFM technology will enable the increased penetration of wind and solar power and is critical to meeting the US administration and COP27 decarbonization goals. Effective collaboration across the various players, especially with OEMs who are expected to deliver these solutions to the market, will ensure that the right solutions are deployed within a fully aligned regulatory and market environment.
Danielle Merfeld, Jason MacDowell and Pedro Arsuaga
GE Renewable Energy
Leave a Reply